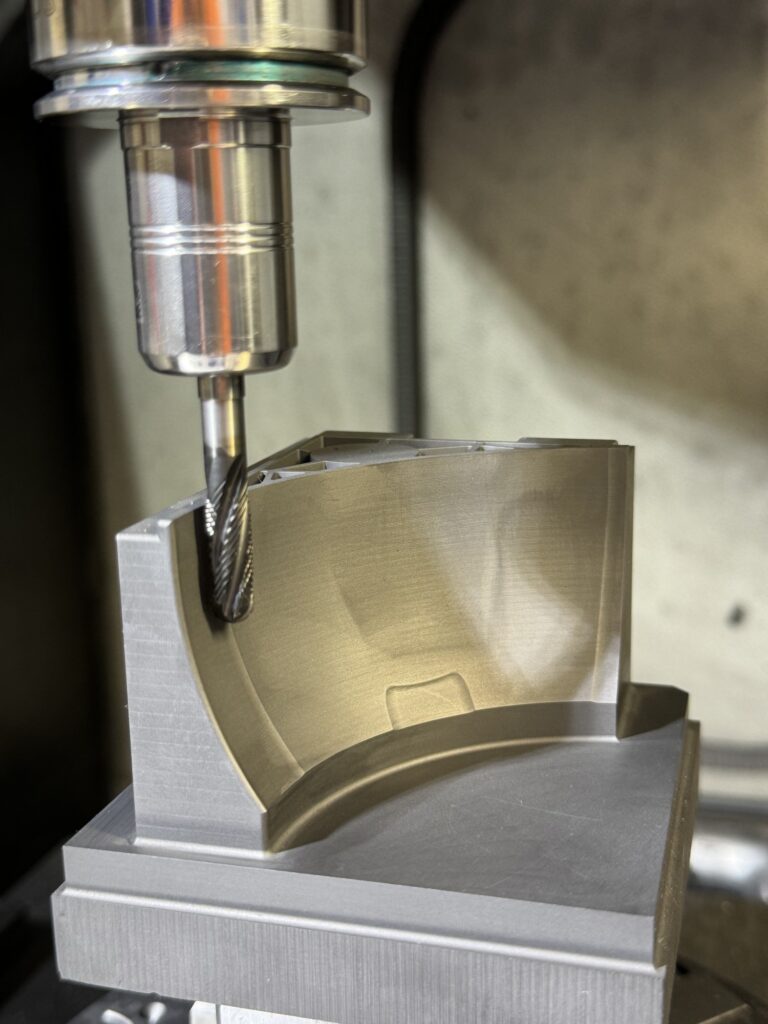
In Fürth werden Spritzgusswerkzeuge für den Einsatz an allen europäischen Standorten der Swoboda Wiggensbach KG konstruiert und gefertigt. Für das häufig eingesetzte Verfahren des Senkerodierens werden die Elektroden aus Graphit selbst hergestellt. Der Prozess schien ausgereift und effizient, bis ein utopisch klingendes Leistungsversprechen zum Test eines Spezialfräswerkzeugs animierte.
„Wir hatten vorher schon andere Werkzeuge ausprobiert und waren mit unserer Wahl zufrieden. Als wir von der Firma Hufschmied Zerspanungssysteme kontaktiert wurden, wollten wir zunächst dankend ablehnen, aber die Behauptung, eine Elektrodenherstellung von elf auf zwei Stunden verkürzen zu können, hatte uns dann aber doch neugierig gemacht“, erinnert sich Florian Kohl, Betriebsleiter Standort Fürth, der Swoboda Wiggensbach KG. Also sollte der Hersteller materialspezifischer Fräswerkzeuge aus Bobingen bei Augsburg den Beweis antreten und bekam eine Elektrode aus einem aktuellen Auftrag geschickt. Thomas Wohlfromm, Technische Beratung und Verkauf, und Andreas Greifenstein, Anwendungstechniker bei Hufschmied Zerspanungssysteme GmbH, stellten sich in einem eintägigen Workshop der Herausforderung in Fürth.
CAM-Strategie wichtig
Frank Förster, Leiter der CAD/CAM-Abteilung bei Swoboda, war angetan vom Vorgehen der Gäste, denn diese starteten mit der gemeinsamen Programmierung der Elektrode in dem bei Swoboda verwendeten CAM-System VISI von Hexagon. „Dass ein Werkzeughersteller so detaillierte Angaben zu Schnittwerten macht und genaue Vorstellungen davon hat, welche Werkzeugwege die besten Ergebnisse bringen, war uns neu. Obwohl Herr Greifenstein normalerweise mit hyperMILL arbeitet, konnte er uns im Workshop auch in VISI noch neue Kniffe zeigen“, so Förster weiter. Schließlich war es so weit, und die EXERON HSC 300 wurde mit dem Graphitbearbeitungswerkzeug Graftor gerüstet, um einen Block Graphit CP 1250 / 5µ zu bearbeiten. Im Gegensatz zu dem vorher bei Swoboda verwendeten zweischneidigen Werkzeug verfügt der Graftor über vier Schneiden mit einer speziellen Geometrie. Die patentierte Vierschneidengeometrie kombiniert Schruppschneiden mit Zähnen und schiebende Schlichtschneiden. Dies sorgt für reduzierte radiale Schnittkräfte an der Spitze, große Laufruhe und ermöglicht das Schruppen und Schlichten mit einem Werkzeug.
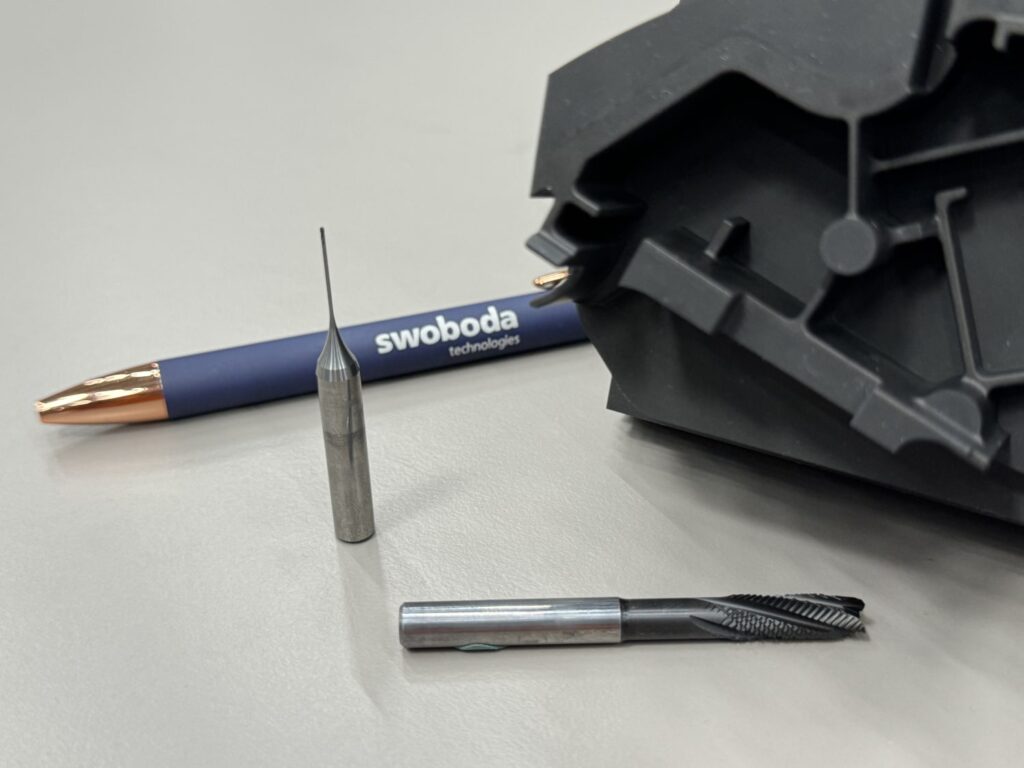
Schon fertig
Die Beispielelektrode hatte bisher knapp elf Stunden Bearbeitungszeit benötigt. Mit dem Hufschmied-Werkzeug war sie nach einer Stunde und vierzig Minuten fertig. Es wurde daraufhin eine Vergleichsmessung durchgeführt. Dabei zeigte sich, dass die mit dem Graftor gefertigte Elektrode teilweise sogar besser war als die Vorlage. Die erreichte Maßhaltigkeit von +-0,005 (+-0,01 ist bei den Elektroden von Swoboda Standard) und auch die Optik waren beindruckend. „Wir waren überzeugt von dem Werkzeug und haben das ganze Sortiment bestellt“, sagt Florian Kohl. „In einem Workshop wurden unsere Mitarbeiterinnen und Mitarbeiter dann mit der optimalen Anwendung vertraut gemacht.“ Frank Förster gibt zu, dass die CAM-Programmierung der Elektroden anspruchsvoller geworden, aber gut zu handhaben ist, weil Hufschmied mit Listen von Aufmaßen, Anstellungen und Vorschüben sehr genaue Vorgaben für die optimale Nutzung seiner Werkzeuge macht. „Man muss zum Beispiel die Vorschübe beachten und Verrundungsradien so weich wie möglich angehen. Die Hufschmied-Werkzeuge sind von Haus aus vibrationsarm, und mit entsprechend weichen Bewegungen erreicht man unglaubliche Geschwindigkeiten“, sagt Frank Förster und gibt ein Beispiel. „Den bisherigen 1 mm Kugelfräser haben wir mit 800er Vorschub gefahren – jetzt fräsen wir mit 2500 m/min.“
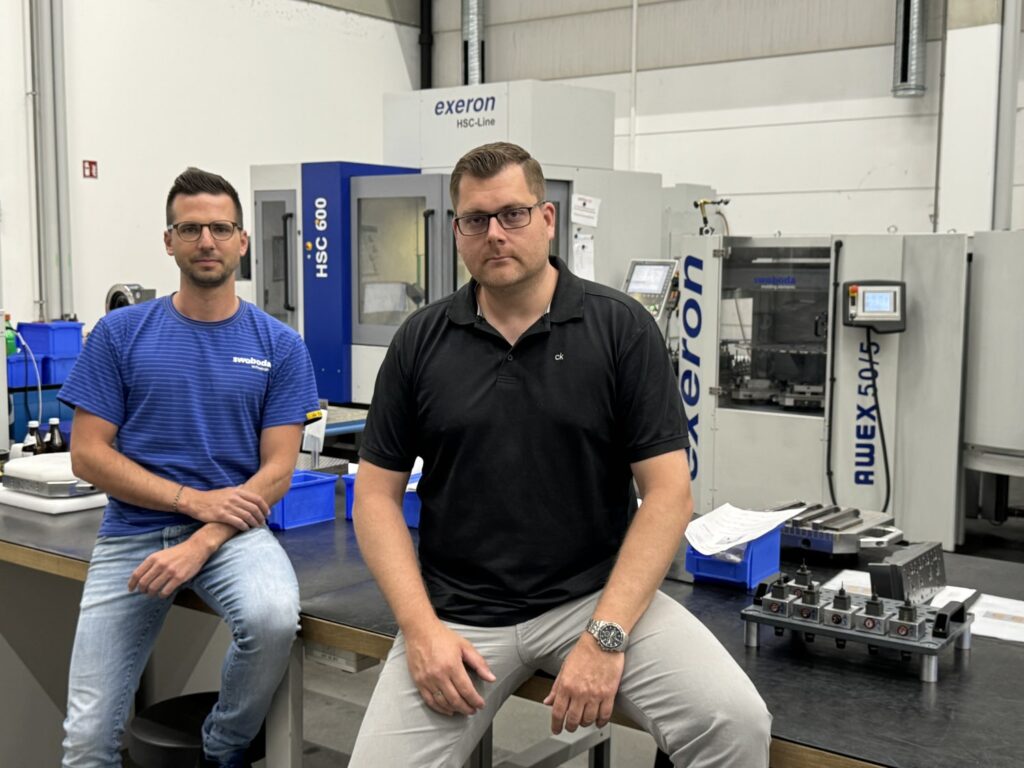
Neue Möglichkeiten
Die Swoboda-Werkzeugbauer haben nach diesen Erfahrungen die Elektrodenproduktion komplett auf die Graftor-Serie umgestellt. Die Schruppschlichtfähigkeit des Werkzeugs verringert potenziell die Zahl der Rüstwechsel, doch nutzt man das bei Swoboda nur teilweise. Stattdessen werden die Werkzeuge 300 bis 400 Minuten zum Schlichten verwendet und danach noch einmal 700 Minuten als Schruppwerkzeug. „Die Standzeiten sind im Prinzip dieselben wie bei den alten Werkzeugen, allerdings mit dem doppelten zurückgelegten Weg“, freut sich Frank Förster.
Dass eine Elektrode jetzt in zwei Stunden gefertigt werden kann, statt in einer Schicht oder länger, eröffnet Swoboda neue Möglichkeiten. Obwohl auch in anderen Märkten aktiv, ist das Unternehmen zu über 90 Prozent Automobilzulieferer. Die oft hohen Ansprüche in der Branche hinsichtlich der Lieferzeiten beeinflussten die Fertigung. Bei Swoboda in Fürth wurde im Werkzeugbau Vieles zerspant, das man, wenn genug Zeit gewesen wäre, auch hätte erodieren können. „Das Erodieren ist interessanter geworden, weil Elektroden jetzt schneller verfügbar sind“, stellt Florian Kohl fest. „Das erhöht insgesamt unsere Flexibilität und Wettbewerbsfähigkeit.“ Dies ist für den Betriebsleiter auch deshalb von großer Bedeutung, weil der Swoboda-Standort Fürth mit seinem 31-köpfigen Team vor zwei Jahren begonnen hat, auch externe Aufträge anzunehmen und dabei ist, dieses Geschäft auszubauen.